22 - Composite Ti-6Al-4V/Polymers Pellets Additive Manufacturing: improvement of the printing parameters to obtain dense and defectless part
Abstract
Composite Ti-6Al-4V/Polymers Pellets Additive Manufacturing: improvement of the printing parameters to obtain dense and defectless part Context In recent years, additive manufacturing has made significant improvements, particularly in the field of polymers and metals, thanks to process like FDM (Filament Deposition Modeling). However, the application of this technology to metals, specifically the titanium alloy Ti6Al4V, remains a complex and costly endeavor, limiting its widespread adoption in this domain. In response to these challenges, PAM technology (Pellets Additive Manufacturing) has emerged, offering a promising alternative using MIM pellets instead of conventional metal filaments, which are both delicate and expensive. This transition to metal pellets significantly decreases the cost of raw materials. One of the key advantages of advancing the PAM process is its ability to manufacture components with complex geometries in a short timeframe at a low cost, making it an attractive option for various applications, including rapid prototyping. While the literature on metal based FDM processes is more extensive, there is still a lack of data to spread the process. This paper seeks to address this gap by focusing on the establishment of optimal parameters to produce parts using Titanium alloy Ti6Al4V from PolyMIM GMBH. Procedure The primary objective is to achieve high reproducibility and good mechanical properties parts with simple geometries by determining printing parameters meeting the requested criteria. The research methodology encompasses a comprehensive range of measurements and evaluations. These include tensile tests, three-point bending tests, microhardness assessments, porosimetry measurements by the Archimede’s principle, dimensional and geometric quality control assessments, roughness measurements, and scanning electron microscopy (SEM) analysis. These rigorous evaluations are crucial for ensuring the quality of the metal parts, both before and after the debinding and sintering processes. Results Printing intricate shapes with high-quality results has proven challenging, primarily due to issues related to adherence. Extensive research endeavors have been undertaken to refine the manufacturing recipe, with a particular focus on optimizing the printing parameters. Especially, it was observed that the manufacturer-specified nozzle temperature of 190°C fell short of the optimal temperature required for successful part production. But in practice, a minimum nozzle temperature of 230°C has proven essential to achieve the desired quality and adherence. The initial recipe find yielded a printed part with a porosity up to approximately 2%.
Speaker
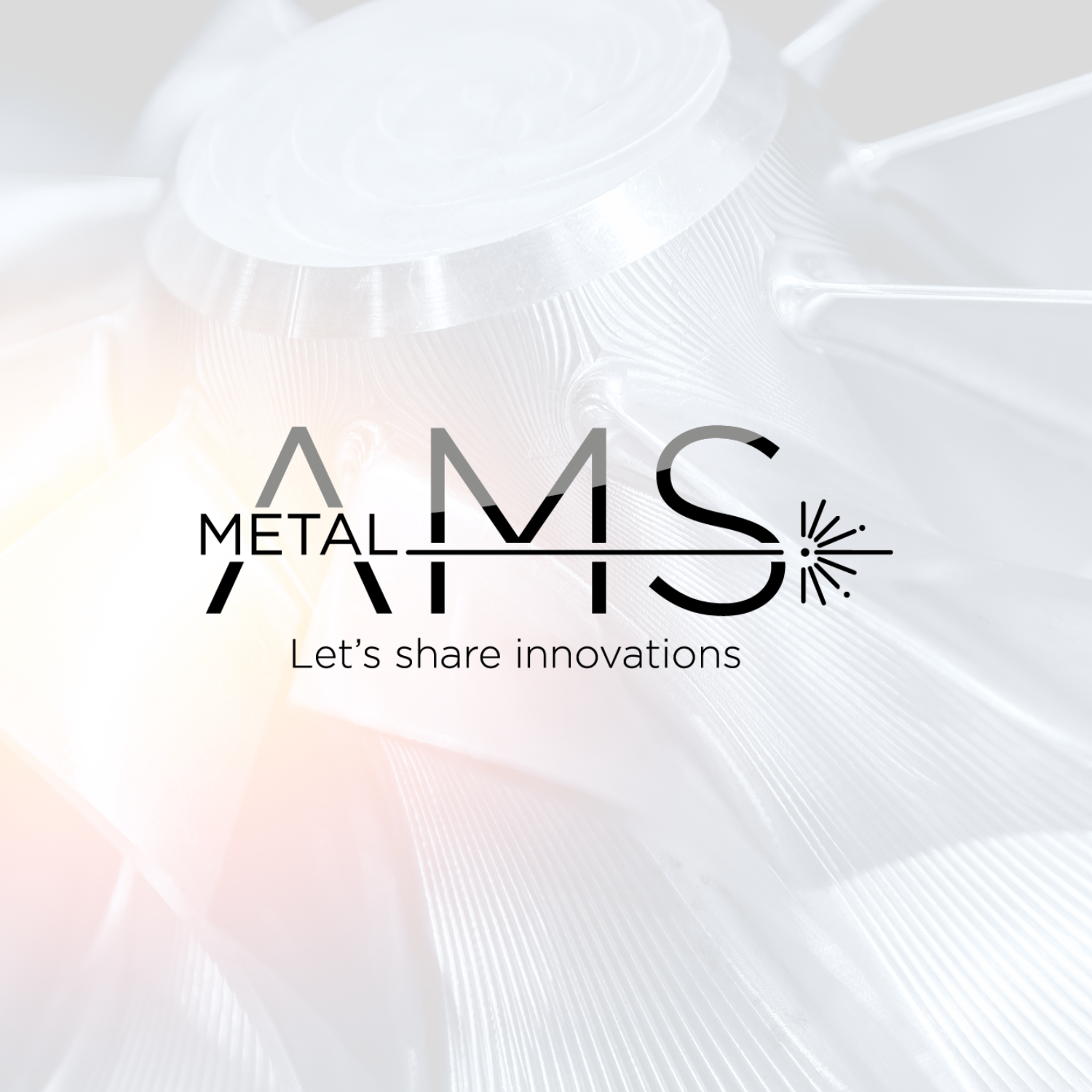
Julien Bossu
Discover speaker profileUniversity of Mons, Mons, Belgium
Conference
22 - Composite Ti-6Al-4V/Polymers Pellets Additive Manufacturing: improvement of the printing parameters to obtain dense and defectless part
Date/Time
20/03/2024
6:00 pm -6:20 pm
Location
Room 7